Subscriber Exclusive
Passing the Weaving Torch
Carol Thilenius details how to weave a 5-shaft pattern on a 4-shaft loom.
Carol Thilenius details how to weave a 5-shaft pattern on a 4-shaft loom. <a href="https://handwovenmagazine.com/passing-the-weaving-torch/">Continue reading.</a>
https://handwovenmagazine.com/cdn-cgi/image/format=auto/https://www.datocms-assets.com/75077/1656656472-passing-the-weaving-torch-header.jpg?auto=format&w=900
“In the old days this weave was rarely attempted on four harnesses but, oddly enough, often on five harnesses, suggesting that weavers of that day may have rigged their four-harness looms with an extra harness to carry the weave threads. This is merely a guess, as I have never found notes or drawings to substantiate it in any of the old books or manuscripts I have examined.”
—Mary Meigs Atwater, The Shuttle-Craft Book of American Hand-Weaving
As weavers, we often look to the past for inspiration and help. We search through old books of drafts and use techniques developed and refined by weavers through the generations. Sometimes, we even write about what we’ve learned hoping that someday our writings will provide inspiration for weavers of the future. This article from *Interweave, Summer 1979, illustrates the strength of those connections between generations of weavers. A technique from the Colonial days piqued the interest of Mary Meigs Atwater. Carol Thilenius became intrigued by Atwater’s suggestion and developed a solution. Finally, Carol’s solution caught the interest of Susan E. Horton, as you can see in her runner in the photo at top.*
SUBSCRIBER EXCLUSIVE
“In the old days this weave was rarely attempted on four harnesses but, oddly enough, often on five harnesses, suggesting that weavers of that day may have rigged their four-harness looms with an extra harness to carry the weave threads. This is merely a guess, as I have never found notes or drawings to substantiate it in any of the old books or manuscripts I have examined.”
—Mary Meigs Atwater, The Shuttle-Craft Book of American Hand-Weaving
As weavers, we often look to the past for inspiration and help. We search through old books of drafts and use techniques developed and refined by weavers through the generations. Sometimes, we even write about what we’ve learned hoping that someday our writings will provide inspiration for weavers of the future. This article from *Interweave, Summer 1979, illustrates the strength of those connections between generations of weavers. A technique from the Colonial days piqued the interest of Mary Meigs Atwater. Carol Thilenius became intrigued by Atwater’s suggestion and developed a solution. Finally, Carol’s solution caught the interest of Susan E. Horton, as you can see in her runner in the photo at top.*
[PAYWALL]
While reading about Bronson weave in Mary Meigs Atwater’s The Shuttle-Craft Book of American Hand-Weaving, the opening paragraph above caught my attention.
This puzzled me. Weavers are notoriously thrifty. If they had used any kind of apparatus they would have kept it for future use. Why was it not passed along to future weavers?
Sometime later the answer popped into my head. It was as if some weaver from the past bent down and said “Don’t be silly, they didn’t need another harness, just a floating warp.”
Atwater noted that this weave was best suited to jack looms and this was the key. Harnesses on a jack loom are either in an “up” or “down” position, holding the warp above or below the level of a floating warp extending between the beams. The floating warp would be independent of the four harnesses, hence acting as a fifth harness.
The idea seemed sound, now it needed testing. I used one of Atwater’s five-harness patterns (see draft) and 5/2 natural pearl cotton sett at 18 epi in a 12-dent reed (sleyed 1-2-1-2). Alternate warps were left as floating warps forming the “tabby” (or “weave”) threads and the others were threaded on the four harnesses to give the pattern. The warping went quickly since only half the warps needed to be threaded through heddles.
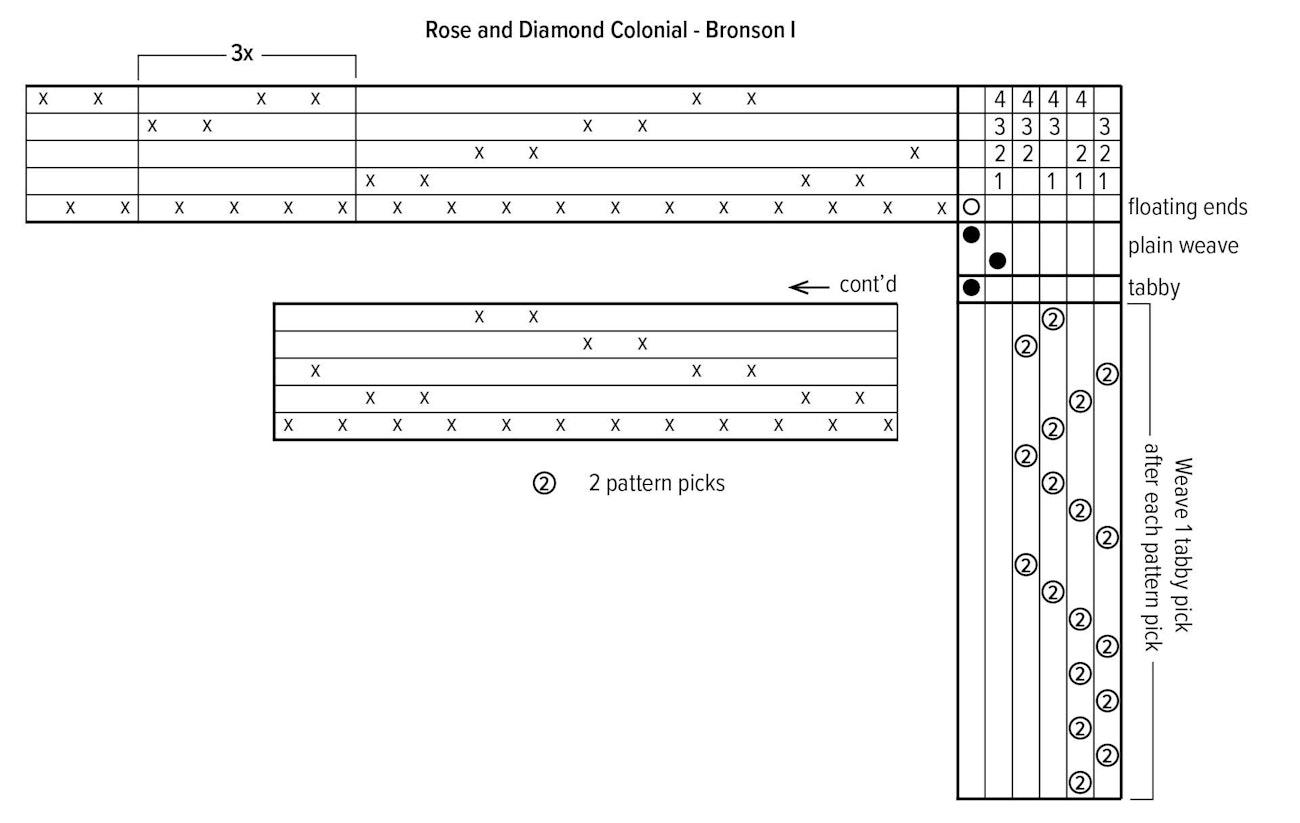
The sheds produced proved to be adequate for a stick shuttle, and the four placemats and table runner wove up quickly. A boat shuttle would be less practical since the size of the shed is about half the normal shed.
To weave a plain tabby, the pattern harnesses were all lifted and the shuttle passed above the floating warps (Photo 1); then the harnesses were all lowered and the shuttle passed below the floating warps (Photo 2).
Photo 1 (Photos by Susan E. Horton)
Photo 2
To produce the pattern, three of the four pattern harnesses were lifted and the shuttle passes between the lifted harnesses and the floating warp (Photo 3); then the harnesses were all lowered for the alternate tabby shot (as in Photo 2).
Photo 3
In all cases the shuttle was passed in the upper shed. This produced weft floats in the pattern area (Photo 4). If warp floats were desired in combination with weft floats, some shots would be in the lower shed, below the floating warps (Photo 3). The chances of picking up or dropping a thread might be greater in that event but should not deter a careful weaver.
Photo 4
The ease of threading and weaving with this phantom fifth harness makes me wonder why it has not been widely used. It surely has applications in other techniques besides Bronson weave.